16. Fabrication [Q&A Session]
-
Full Access
-
Onsite Student Access
-
Virtual Full Access
Date/Time: 06 – 17 December 2021
All presentations are available in the virtual platform on-demand.
Computational Design of Planar Multistable Compliant Structures
Abstract: This paper presents a method for designing planar multistable compliant structures. Given a sequence of desired stable states and the corresponding poses of the structure, we identify the topology and geometric realization of a mechanism—consisting of bars and joints—that is able to physically reproduce the desired multistable behavior. In order to solve this problem efficiently, we build on insights from minimally rigid graph theory to identify simple but effective topologies for the mechanism. We then optimize its geometric parameters, such as joint positions and bar lengths, to obtain correct transitions between the given poses. Simultaneously, we ensure adequate stability of each pose based on an effective approximate error metric related to the elastic energy Hessian of the bars in the mechanism. As demonstrated by our results, we obtain functional multistable mechanisms of manageable complexity that can be fabricated using 3D printing. Further, we evaluated the effectiveness of our method on a large number of examples in the simulation and fabricated several physical prototypes.
Author(s)/Presenter(s):
Generalized Deployable Elastic Geodesic Grids
Abstract: Given a designer created free-form surface in 3d space, our method computes a grid composed of elastic elements which are completely planar and straight. Only by fixing the ends of the planar elements to appropriate locations, the 2d grid bends and approximates the given 3d surface. Our method is based purely on the notions from differential geometry of curves and surfaces and avoids any physical simulations. In particular, we introduce a well-defined elastic grid energy functional that allows identifying networks of curves that minimize the bending energy and at the same time nestle to the provided input surface well. Further, we generalize the concept of such grids to cases where the boundary of the surface does not need to be convex, which allows for the creation of sophisticated and visually pleasing shapes. The algorithm finally ensures that the 2d grid is perfectly planar, making the resulting gridshells inexpensive, easy to fabricate, transport, assemble, and finally also to deploy. Additionally, since the whole structure is pre-strained, it also comes with load-bearing capabilities. We evaluate our method using physical simulation and we also provide a full fabrication pipeline for desktop-size models and present multiple examples of surfaces with elliptic and hyperbolic curvature regions. Our method is meant as a tool for quick prototyping for designers, architects, and engineers since it is very fast and results can be obtained in a matter of seconds.
Author(s)/Presenter(s):
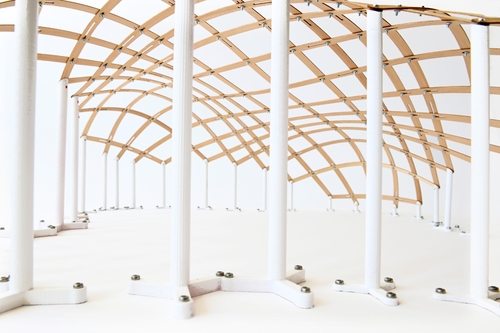
Optimizing Contact-based Assemblies
Abstract: Modern fabrication methods have greatly simplified manufacturing of complex free-form shapes at an affordable cost, and opened up new possibilities for improving functionality and customization through automatic optimization, shape optimization in particular. However, most existing shape optimization methods focus on single parts. In this work, we focus on supporting shape optimization for assemblies, more specifically, assemblies that are held together by contact and friction. Examples of which include furniture joints, construction set assemblies, certain types of prosthetic devices and many other. To enable this optimization, we present a framework supporting robust and accurate optimization of a number of important functionals, while enforcing constraints essential for assembly functionality: weight, stress, difficulty of putting the assembly together, and how reliably it stays together. Our framework is based on smoothed formulation of elasticity equations with contact, analytically derived shape derivatives, and robust remeshing to enable large changes of shape, and at the same time, maintain accuracy. We demonstrate the improvements it can achieve for a number of computational and experimental examples.
Author(s)/Presenter(s):

Spatial-Temporal Motion Control via Composite Cam-follower Mechanisms
Abstract: Motion control, both on the trajectory and timing, is crucial for mechanical automata to perform functionalities such as walking and entertaining. We present composite cam-follower mechanisms that can control their spatialtemporal motions to exactly follow trajectories and timings specified by users, and propose a computational technique to model, design, and optimize these mechanisms. The building blocks of our mechanisms are a new kind of cam-follower mechanism with a modified joint, in which the follower can perform spatial motion on a planar, cylindrical, or spherical surface controlled by the 3D cam’s profile. We parameterize the geometry of these cam-follower mechanisms, formulate analytical equations to model their kinematics and dynamics, and present a method to combine multiple camfollower mechanisms into a working mechanism. Taking this modeling as a foundation, we propose a computational approach to designing and optimizing the geometry and layout of composite cam-follower mechanisms, with an objective of performing target spatial-temporal motions driving by a small motor torque. We demonstrate the effectiveness of our technique by designing different kinds of personalized automata and showing results not attainable by conventional mechanisms.
Author(s)/Presenter(s):
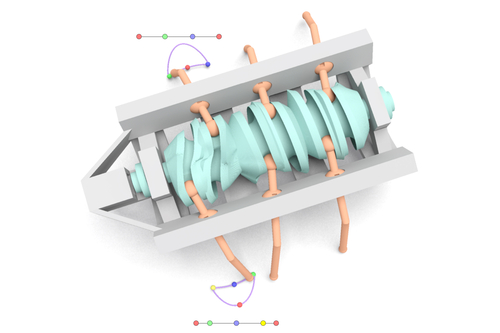
Volume decomposition for two-piece rigid casting
Abstract: We introduce a novel technique to automatically decompose an input object's volume into a set of parts that can be represented by two opposite height fields. Such decomposition enables the manufacturing of individual parts using two-piece reusable rigid molds. Our decomposition strategy relies on a new energy formulation that utilizes a pre-computed signal on the mesh volume representing the accessibility for a predefined set of extraction directions. Thanks to this novel formulation, our method allows to efficiently optimize for a fabrication-aware partitioning of volumes in a completely automatic way. We demonstrate the efficacy of our approach by generating valid volume partitionings for a wide range of complex objects and physically reproducing several of them.
Author(s)/Presenter(s):
